6 Essential Steps to Prepare HVAC & Plumbing Systems for Winter Weather
By Sean Comerford
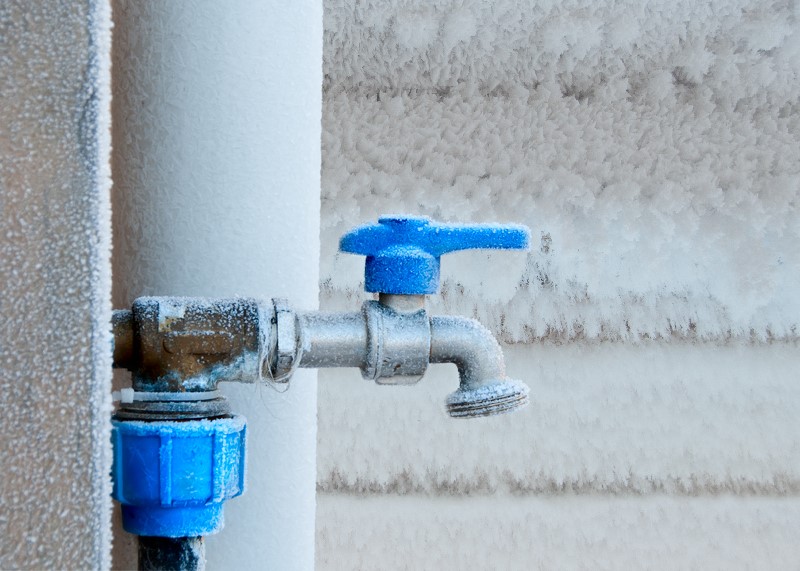
Winter weather conditions are fast approaching, so it’s time to prepare plumbing and heating systems to withstand the elements. Whether a seasoned trade professional, a skilled do-it-yourselfer, or a cost-conscious property manager, the following are tips to keep systems running safely and smoothly this winter.
Tip 1: Visually inspect hydronic heating systems for leaks and buildup
Checking a building’s hydronic heating systems during the summer and fall months is a great way to conduct routine maintenance and detect problems before the bitter cold hits. Start by conducting a visual inspection of the area where the boiler sits. Look for any visible signs of potential leaks — such as wet spots in the concrete or pooling water. If there is an older model that utilizes baseboard or radiator heating, the system should be run to inspect leaks.
There are chemical system cleaners on the market that can clean and condition steam and hot water boilers, as well as hydronic heating systems in general. These chemical cleaners help maximize system efficiencies and use silicones to protect pumps by lubricating seals. Including system cleaners in a preliminary winterization check can prevent dirt, rust and sludge, as well as prime a system for antifreeze.
Visual inspections are also an opportune time to check a building’s forced-air HVAC system, especially the registers and grilles for dirt or buildup.
Regular filter replacement is crucial to maintain system efficiency. Leaving filters in too long can result in heating systems utilizing more energy to push air through the system due to contaminant buildup. Generally, it is advised to replace filters every three months, but defer to filter manufacturer recommendations. Health regulations may require specific types of businesses — like hospitals — to replace filters more frequently.
Tip 2: Introduce inhibitors to hydronic heating systems
Inhibitors are chemicals added to heating and boiler systems that prevent rust and corrosion. When added to heating systems, inhibitors may help increase efficiency and performance. As previously mentioned, a corroded or rusted pipe can lead to product buildup, leaks and a 15% decrease in system performance due to the buildup decreasing the pipe’s internal circumference.
Depending on the issue, many different types of products target specific problems in heating systems. To decide which product is needed, collect a water sample from the drain valve and test for rust, corrosion, scale, sludge and pH and glycol levels.
Tip 3: Check antifreeze and pH levels in closed-loop systems
Another step to prepare for winter is to check the antifreeze levels in closed-loop water systems. Freeze-protection and corrosion-protection levels should be checked annually.
It is essential first to determine the desired temperature coverage for a system and match it to the appropriate product concentrations provided by the antifreeze manufacturer. Late summer or early fall would be an ideal time to run these checks, particularly for buildings that are vacant on the weekends.
Testing ensures the system’s pH levels are correct. If they fall too low (the acidic end of the pH spectrum), metal components within the heating system can begin to corrode. One way to solve this issue is to introduce chemical additives that will re-balance PH levels in heating systems.
Avoiding corrosion is essential to maintaining the health of hydronic heating systems. Corroded pipes will lead to buildup and rust. That, in turn, will cause leaks down the line. Similar to dirty filters in forced-air HVAC systems, rust buildup in copper and steel piping in a hydronic system will slowly restrict the flow, forcing the system to overcompensate for escaping heat. As a result, more energy is used to heat rooms, resulting in higher fuel bills.
Tip 4: Clean out gutters and inspect roofing
Preparing for winter weather involves more than handling freezing temperatures. Heavy winter storms can bring large amounts of snow or rain, making roofing and gutter systems vulnerable. Property managers should conduct preliminary inspections to locate and repair leaks and clean gutters. Dirty gutters can lead to clogs, causing flooded areas and the system to run inefficiently.
To properly clean gutter systems, remove large debris, like leaves and twigs, by hand; use a gutter scoop to remove compacted trash. Once cleaned, flush gutters with water to check for clogs. Subsequently, check drains for proper flow and drainage, paying specific attention to any leaks at the seams.
Tip 5: Make sure irrigation systems are winterized
The end of fall is a perfect time to prepare irrigation systems for winter. To be properly winterized, these lines need to be cleared and drained. Depending on the type of system installed, there are three primary ways to drain an irrigation system: manual drainage, automatic drainage and blow-out drainage. The blow-out method is most suitable for larger irrigation systems and uses an air compressor to force out any remaining water and air.
Failure to properly winterize irrigation lines can have costly ramifications. As the ground freezes during the winter, irrigation lines with any remaining water can expand; if made from non-pliable materials like PVC, the expanded frozen water can lead to cracks.
These cracks pose an issue when irrigation systems are reactivated during the spring and summer months. As a result of the damage, water will continually run, forming small ponds as the water is reintroduced to the system.
Tip 6: Manually shut off hose bibs
While many commercial hose bibs are frost-proofed, some systems require manual shut-offs in preparation for winter months. Similar to irrigation systems, trapped water in these pipes during the winter will freeze, expand and create cracks, which can turn into leaks.
Failure to properly winterize hose bibs can cause more significant issues once it’s time to use these systems again in warm weather. Improper winterization can cause water to pool behind walls. To remedy this, create an opening in the wall, assess potential water damage and subsequently fix both the damage and the wall.
In some cases, manual shut-offs are not an option. Adding insulation or a louvered vent will ensure warm air can reach these areas to prevent freezing.
By following the aforementioned steps, HVAC and plumbing equipment and systems will be well prepared for winter conditions.
Sean Comerford is a technical applications manager at Oatey Co. He is a third-generation tradesman with nearly 20 years of plumbing experience.