Practical Tips for Preparing Commercial HVAC Systems for Winter Weather
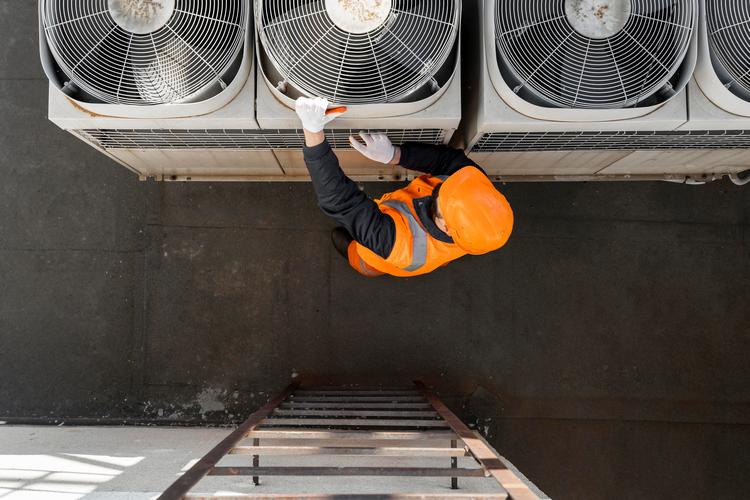
By Andy Peters
With summer in the rearview mirror, now is the time to think about preparing HVAC systems for winter weather. Proper maintenance is crucial to getting the most efficiency out of and prolonging the life of commercial HVAC solutions. The following are some tips to make both conventional and VRF HVAC systems winter-ready.
Perform bi-yearly maintenance
Fall and spring are the best times to ensure HVAC systems are running properly because they are not used as much during these seasons. However, busy building managers can overlook scheduling these bi-yearly appointments. Contractors should make a point of reaching out to commercial customers to remind them to schedule these appointments.
They can educate customers on the risks of what may happen if the HVAC system is not serviced: costly breakdowns, increased energy bills, reduced heating ability and discomfort for occupants if the HVAC system fails during low temperatures.
When performing a preventive maintenance check, look at the following parts for conventional HVAC systems:
- Filters – Check the air filters and clean and replace them if needed.
- Refrigerant – Check the refrigerant levels and look at the whole system for any leaks.
- Electrical – Make sure all electrical connections are secure and are not frayed or damaged.
- Unsafe leaks – Monitor for any carbon monoxide or gas leaks.
- Coils – Clean the condenser and evaporator coils.
- Drains – Check drains for any blockages.
- Flue – Clean and check the flue system and its attachment to the furnace.
- Lubrication – Lubricate any moving parts.
A full checklist for preventive winter maintenance is longer, but these are some of the most important steps a contractor can take to ensure a conventional commercial HVAC system is ready to face the winter months ahead.
VRF preventive maintenance tips to consider
Commercial buildings are increasingly using variable refrigerant flow heat pump systems for heating and air-conditioning needs. VRF technology is a fast growing segment of the commercial HVAC industry. For those not familiar with VRF systems, they do not use fossil fuels. Instead, an all-electric, highly efficient VRF system provides heating and cooling by cycling refrigerant between an outdoor unit and each zone’s ductless or ducted indoor unit. Up to 50 indoor units can connect to a single outdoor unit.
Many tips that I laid out for conventional HVAC systems still apply for VRF technology. However, bi-yearly maintenance for VRF units is a little more complicated. It’s well worth the effort because of their energy efficiency. Below is a checklist my team follows during preventive maintenance appointments for VRF:
- Refrigerant leaks – Detect and fix any leaks and check the refrigerant levels.
- Voltage – Make sure the voltage readings align with what is listed on the HVAC system’s nameplate.
- Compressor ohms – Test the electrical resistance. The resistance is influenced by several factors, including the condition of the motor windings, the temperature and the material of the components.
- Compressor amps – Measure each compressor’s amps to understand whether the amount of electrical current is sufficient.
- Crankcase heater – Ensure this vital part of the system is running as it should.
Additional best practices include checking the high-side pressure to make sure it’s in the right range. If too low, there could be a leak in the system; when too high, the compressor could overheat and fail. Similarly, check the low-side pressure. Often referred to as suction pressure, optimal low-side pressure helps smooth refrigerant transition and effective cooling. Lastly, test the discharge temperature to ensure the compressor functions as it should.
Install snow and hail guards
One more equipment tip that applies across HVAC types is this: winter-weather-protection systems like snow and hail guards can help safeguard heat pump systems. Snow and ice can accumulate, and these guards protect the integrity of the outdoor equipment. If contractors in northern climates see commercial HVAC systems without these parts, they should strongly recommend them to building managers.
Ongoing training is foundational
Of course, all the checklists and useful equipment in the world are not going to help contractors who don’t have the proper training. Continuous training is vital, and it’s ingrained in me from my time in the U.S. Navy. That’s why every two years, the technicians who work for me take hands-on training from the manufacturers of the heat pump systems we install and maintain. Only with this regular training are they ready to confidently face winter maintenance challenges.
Planning ahead is planning for success
Winter is not the time for a commercial building’s HVAC solution to go out. It’s always best to troubleshoot and perform maintenance before temperatures reach freezing.
To prepare for winter, contractors should focus on upkeep, installing snow and hail guards and ensuring their team of HVAC technicians have ongoing training. Doing so will help ensure building occupants stay warm and comfortable even during the coldest months.
Stephen Andrew (Andy) Peters is principal at both VRF Technologies and VRF & VRV Consulting Investigation. He has over 20 years of experience in the HVAC industry and is a Diamond Commercial Contractor® and a Diamond Contractor®, groups of specially trained professionals qualified to install Mitsubishi Electric HVAC equipment.
Image by freepik