But It’s Just Water, Isn’t It?
Evolution of developing a water quality standard for hydronic systems
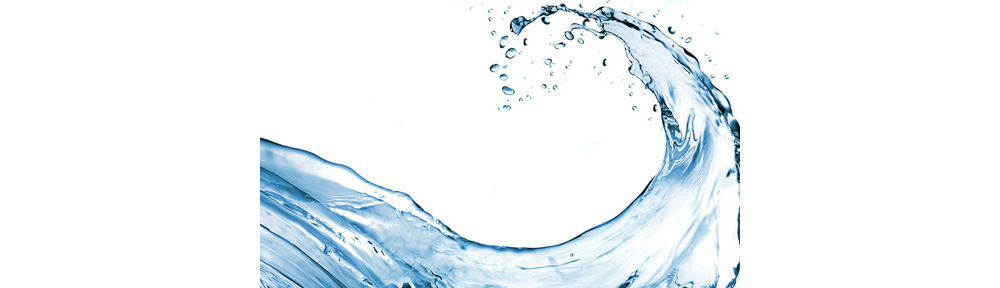
By Mark Eatherton
During the late, great Les Nelson’s last AHR conference in Chicago, Illinois back in 2018, he asked me what the hydronics industry needed the most. He was on a mission to increase the visibility of the Radiant Professionals Alliance and give the industry something it could really use. At the time, I was the service manager for a large hydronic concern in Colorado. We had just replaced a bunch of mechanical equipment on a large complex that had failed within its warranty coverage period. The equipment manufacturer had required a copy of the water quality analysis report for the property.
They wanted to see the pH, total dissolved solids, conductivity, oxygen content, total suspended solids and concentration of chlorides.
Fortunately, when this system was originally sold, it included a comprehensive water treatment program utilizing some chemicals that ensured we were in compliance with the companies’ water quality standards. Prior to this time, closed-loop system water quality was not top of mind as it pertained to closed-loop hydronic systems. The general attitude of hydronic contractors was, “It’s just water, isn’t it?”
For hundreds of years, the equipment employed for hydronic systems had very thick walls. The boilers and the heat emitters were made of thick cast iron. It was accepted that some parent material would be lost to oxidation without compromising the heat exchangers integrity. In fact, it was thought that if the water was black, it was considered “plumbers’ black gold” and was an indication the residual oxygen had been consumed through the process of oxidation and the water was considered “dead.”
As it pertained to piping and distribution systems, most of these older systems also utilized metal pipes (steel, copper, cast iron fittings) and the systems were not subject to oxygen diffusion through the walls of the tubing or pipes used to transport these fluids through the systems. The times, they are a changin’.
Today’s systems are comprised of various metals including different classifications of stainless steel, steel, aluminum, copper, cast iron and a significant amount of plastic tubing, which allow oxygen to diffuse through the walls of the tubing. So, with all of this in mind, I told Les that the industry badly needed a water quality standard for closed-loop hydronic systems. He said he’d begin the process of filing the necessary paperwork to get this initial concept under development for a recognized national standard. Unfortunately, Les passed away before we were able to assemble the necessary brain power to construct the standard. But it did not end there. We moved the effort forward with the support and help of the good folks at IAPMO.
Participants were solicited, and a large group of affected industries was well represented from throughout the industry, including equipment manufacturers, tubing manufacturers, chemical manufacturers, system designer/engineers, equipment manufacturer representatives, labor unions and installing contractors.
All told, the initial solicitation ended up with 23 people representing all facets of the industry from both North American and European concerns. Europe is many years ahead of North America as it pertains to having an actual standard. In fact, we reviewed numerous relevant documents and considered the research that produced them in our own development of the new standard.
We met several times between August 2020 and August 2021 and assembled this standard, known as American National Standards Institute/IAPMO H1001.1, Standard for Quality of Heat Transfer Fluids Used in Hydronics Systems.
After many hours of meeting, the final standard included both a chemical and nonchemical treatment program. The process of developing this standard included a public review/comment period to give industry peers the opportunity to review the standard and to make public comments as it pertained to the standard. After this rigorous process was completed, the standard was accepted and the necessary paperwork put in place to make it an ANSI/IAPMO standard.
It is the hope of the committee that this standard will be adopted by jurisdictions to ensure that the standard is put in place and provide guidance for contractors responsible for designing, installing and maintaining these systems. Adoption of the standard will also provide warranty protection to the consumer to ensure their systems’ warranty is kept intact.
In the end, the standard can be adopted by individual contractors looking to enhance their position within the industry. The standard was dedicated to the memory of Les Nelson, a tireless warrior for the hydronics industry.
For more information or to purchase a copy of the standard, visit https://iapmomembership.org/store/iapmo-ansi-h1001-1-2021/1142/.
Thank you to all of the participants and IAPMO staff who helped to produce this comprehensive standard. And thank you to Les Nelson for having the foresight to help further the hydronics industry.
Mark Eatherton is chairman of the IAPMO/ANSI H1001.1 Committee.